Tailored Solutions for Electronic Devices’ Protection
Custom Foam Parts: Tailored Solutions for Your Electronics
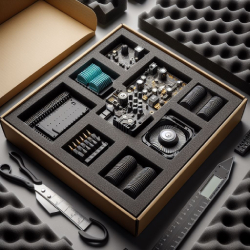
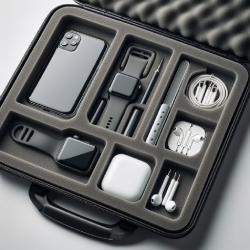
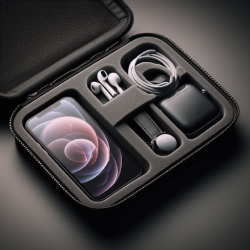
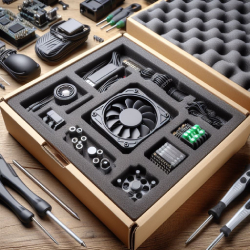
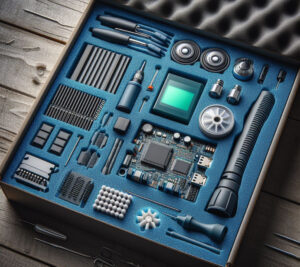
Applications of Electronic Foam
The versatility of electronic foam solutions extends across multiple industries, contributing significantly to various domains:
Confirm your order today and experience our dedication to delivering top-quality, customized foam packaging solutions tailored to your specific electronic needs.
Contact us to discuss how we can safeguard your electronic components during transit with reliable foam packaging solutions
Why Custom Foam Parts for Your Electronics Packaging?
Customization
Each electronic component demands specific packaging solutions. Our team collaborates closely with you to create packaging for electronics with foam inserts that snugly fit your products, ensuring optimal protection and security.
Quality Materials
We use premium packaging materials for electronics known for durability and exceptional shock absorption, ensuring the safety of your electronic components during transit.
Expertise:
With years of experience in electronics manufacturing, we possess extensive knowledge in designing foam packaging for various electronic components. Our expertise enables us to deliver innovative and effective packaging solutions.
Precision Engineering:
Our manufacturing processes are characterized by precision and meticulous attention to detail. Leveraging cutting-edge technology and skilled craftsmanship, we create foam packaging that offers maximum protection and minimal movement.
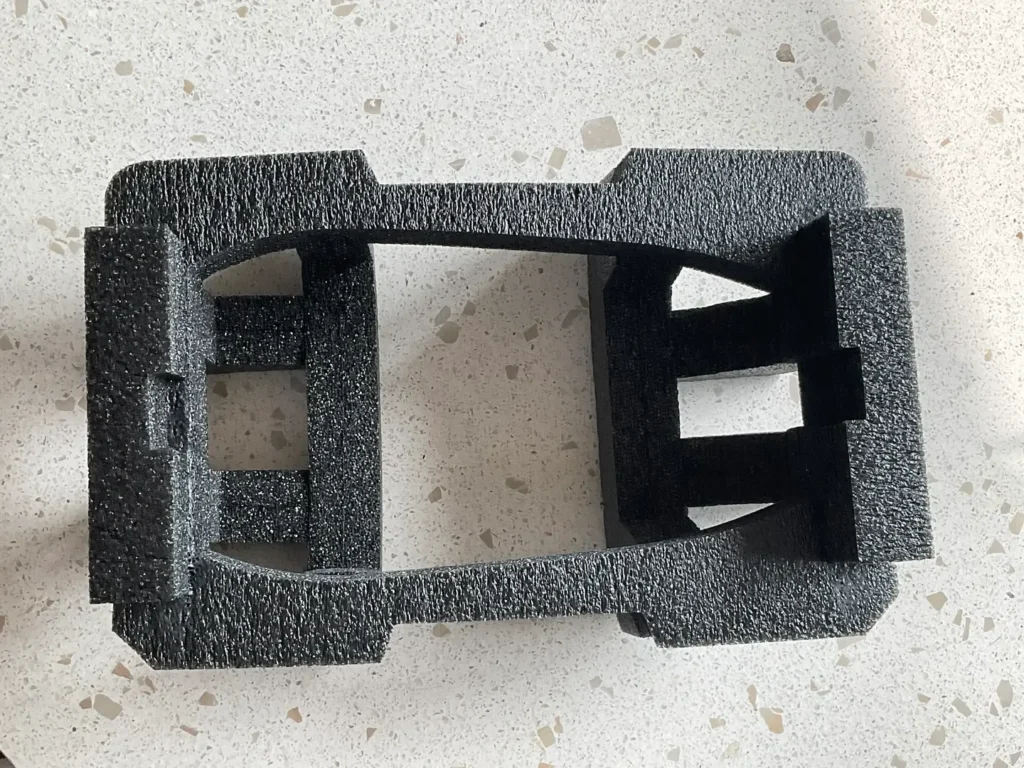